Timpani, Kick drums, kettle drums, these are all great examples of instruments that inspired the innovation of Wilson Benesch infrasonic technologies. Each musical instrument creates low frequency sound with attack and dynamics that hit you in the chest.
The IGx seeks to recreate this experience of live music using innovative technologies including the push-pull motor design, a rounded geometric enclosure that mimics these instruments and a super lightweight Carbon Fibre – Polyethylene Terephthalate diaphragm. By combining these highly evolved technologies, Wilson Benesch deliver the ultimate solution – lightning fast, highly integrated, perfectly resolved low frequency sound that physically moves the listener.
Launched in 2006, the original Torus Infrasonic Generator remains a significant departure from all prior art. Unlike all design’s prior, the Wilson Benesch Torus Infrasonic Generator eliminated the cabinet from any and all structural responsibilities. Instead, Wilson Benesch placed a 16kg Steel Core at the heart of the Torus Infrasonic Generator. The core legislates that all energy from the two push-pull Neodymium motors is grounded. Ingeniously simple. Totally unique.
Through collaboration with two leading companies in the field of fibre weaving and composite design, a new fabric was invented to achieve what was previously impossible. The Carbon Fibre – Polyethylene Terephthalate diaphragm is geometrically optimised and realised from a woven material that incorporates both the fibre as well as the resin matrix. This material is woven exclusively in Europe for Wilson Benesch. The geometrically optimised, sub-100g, Carbon Fibre – Polyethylene Terephthalate diaphragm is a marvel of engineering. The lightweight diaphragm can support 1000 times its own mass, a testament to the stiffness of the structure. The diaphragm at the heart of the new IGx sets the industry standard both in terms of stiffness and damping. It is a peerless solution that enables the reproduction of lightning-fast Timpani.
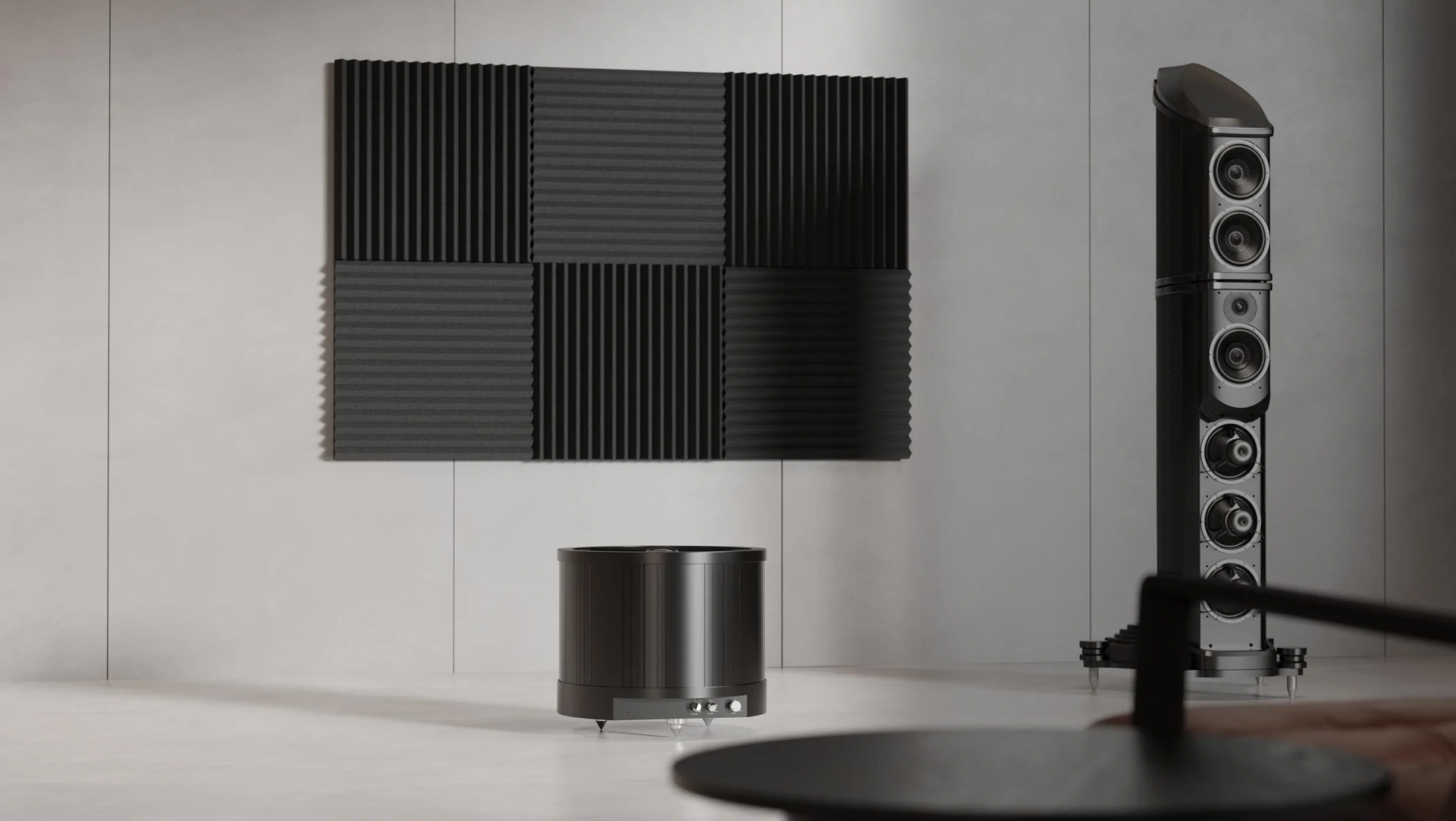
Inspired by the instruments that it aspires to reproduce, the IGx’s circular external structure is the geometrically perfect shape. The absence of flat panels or material redundancy is notable, taking its place is the curvature that defies cabinet resonance, a perfect example of form follows function.
The new IGx represents a new level of refinement, quality and performance. Delivering music enthusiasts a new level of low frequency sound reproduction within their personal home audio system.
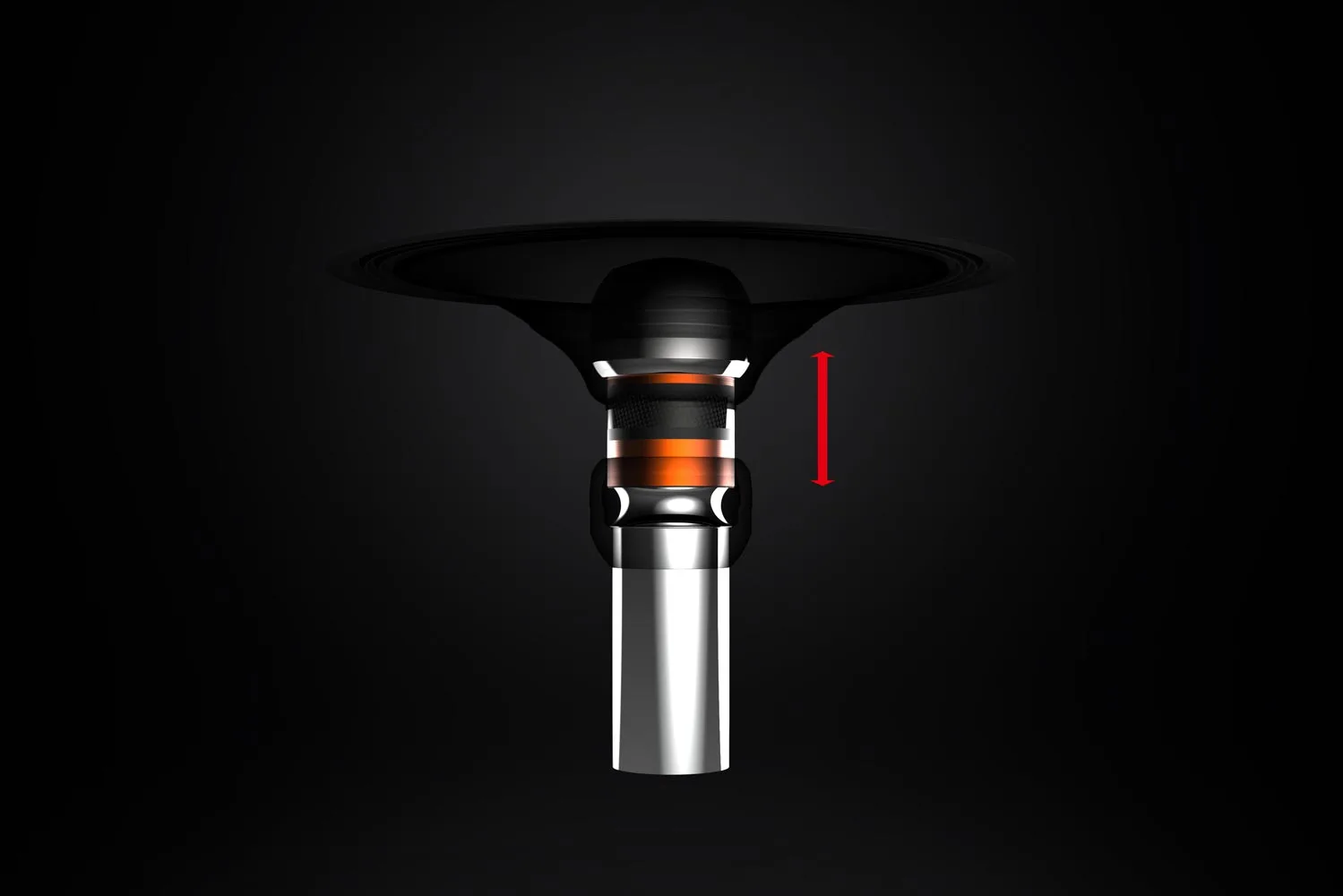
Electromagnetic Motor
At the heart of the IGx there is no dynamic drive unit in the conventional sense.
A conventional dynamic drive unit places a diaphragm inside a basket with a voice coil that is connected to a stiff spider at the centre of the basket structure that controls the position of the diaphragm with a rubber surround that connects to the basket perimeter.
Conversely the IGx does not have a basket at all, during playback the position of the lightweight diaphragm is dictated to and controlled by two 82mm voice coils and two high power NdFeB magnets that operate in a push-pull formation. One coil and one magnet sits directly above the diaphragm forming the visible chrome cap at the centre of the diaphragm, whilst a second coil and second magnet is on the underside of the diaphragm inside the IGx. The two magnets and coils in turn reside around a huge steel core that is placed in the centre of the IGx in the vertical axis.
The IGx still has a spider and a surround, but the position of the cone is dictated to by a push pull electromagnetic motor, therefore overcoming the need for super stiff spiders and suspensions required in a conventional subwoofer design. A very stiff spider and surround resist and retard the movement of the diaphragm, so because the IGx does not have to overcome such resistive elements the movement of the lightweight diaphragm is extremely efficient. Wilson Benesch have observed the basic laws of physics and through thoughtful design created a low frequency woofer that does not require thousands of watts from an amplifier, whilst still being the industry reference in terms of step response and dynamics.
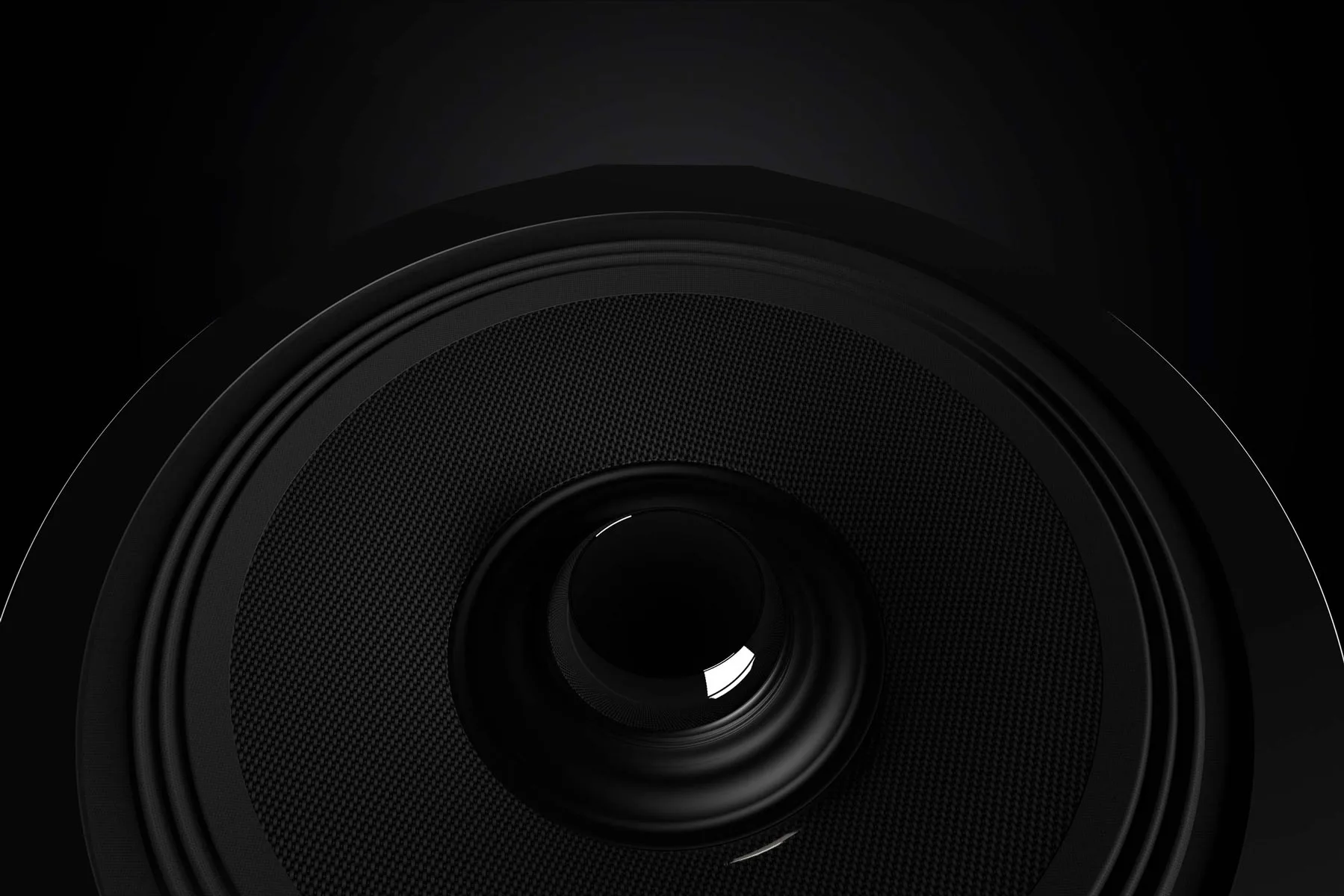
18″ CARBON FIBRE – PET DIAPHRAGM
A completely bespoke Carbon Fibre – PET fabric was developed by Wilson Benesch during the development of the original Torus Infrasonic Generator. This fabric is woven in Europe exclusively for WB.
The CF-PET fabric delivers multiple advantages. It allows WB to form the complex highly optimised toroidal geometry of the IGx diaphragm from a single piece of fabric and not a patchwork of carbon fibre pre-preg. This in turn derives maximum stiffness, maximum damping and optimal energy flow down the fibre. The IGx 18” diaphragm is the stiffest, lightest, and most highly damped dynamic drive unit diaphragm ever made. The IGx diaphragm weighs less than 100g but it is able to support one thousand times its own mass, a testament to the stiffness of the structure.
If fidelity is accuracy, then within a system that is recreating a recorded piece of music, timing is fidelity. Any delay in the drive unit diaphragm transient response to the signal that it is delivered by the amplifier is a loss of fidelity.
Thus the design of the IGx is highly optimised, being both stiff and light, the IGx 18” diaphragm is able to maintain pistonic movements of air to create low frequency infrasonic sound that is perfectly timed, whilst also not distorting thanks to the unique damping properties of the CF-PET material.
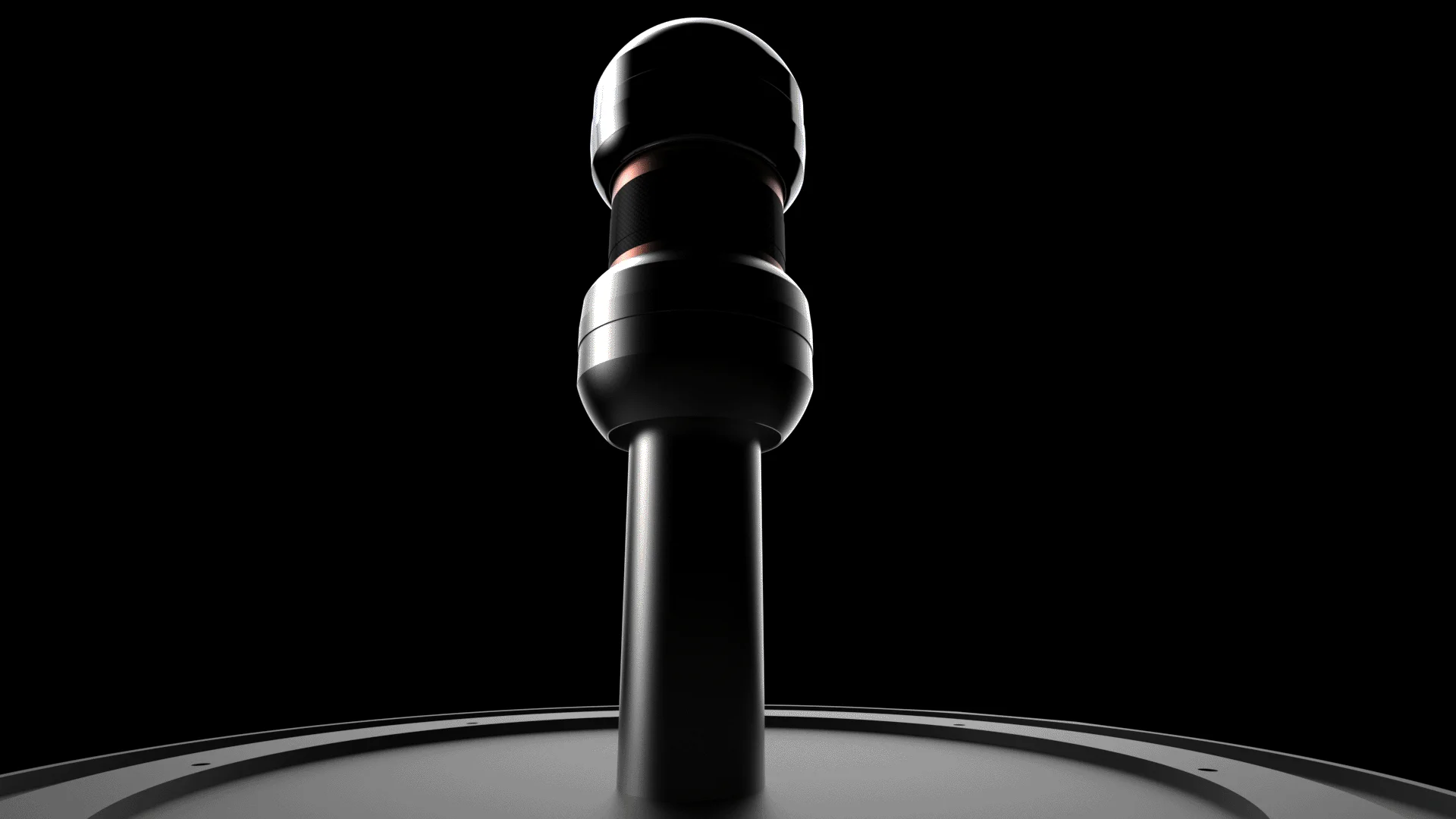
THE CORE
A dual motor push/pull drive system consists of two sets of 82mm diameter voice coils that are deployed in front of and behind an 18″ CF-PET diaphragm around a massive 16kg precision machined central core containing high energy rare-earth magnets. The coils use non-commercially available but incredibly high heat conducting boron nitride, and the core conducts all the heat and structural borne resonant energy directly to the ground bypassing the cabinet.
The are multiple other benefits to the Core:
1. It eliminates the requirement for a stiff spider to dictate the position of the diaphragm.
2. Instead the position of the diaphragm is dictated to electro-magnetically by two rare-earth high power magnets driving two coils in a push-pull formation.
3. Efficiency, because the IGx is not having to overcome the spider which induces latency and massive inefficiency in the use of the power of the amplifier to overcome the stiffness of the spider, the energy provided by the amplifier is used efficiently to drive a lightweight carbon fibre diaphragm.
4. Almost all of the energy generated in the IGx enclosure is placed directly through a central steel core.
5. The Steel Core is placed in the vertical axis, this ensures that all the moving components of the IGx are moving through the gravitational plane.
6. The steel core is also one huge heat sink, it is able to absorb the large amounts of heat that the two coils create.
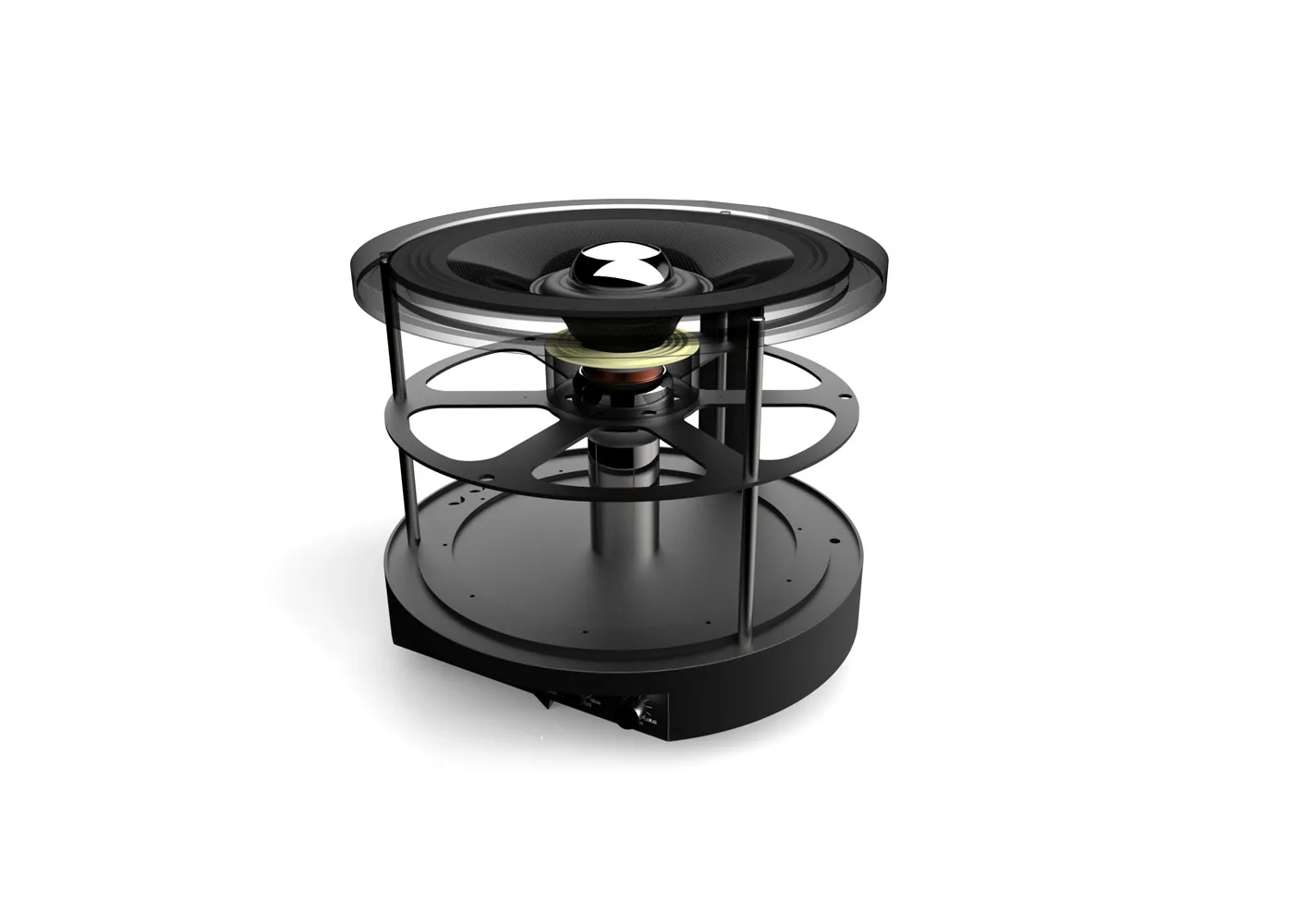
HORIZONTAL & VERTICAL CROSS BRACING
The IGx has a geometrically optimised circular drum like form. This provides maximum stiffness across the external structure. But in addition to this, Wilson Benesch have engineered the IGx with a added stiffness and damping across the horizontal and vertical axis of the IGx.
A large 10mm diameter steel ring is placed across the centre of the horizontal axis. This interfaces with all of the side panels that form the IGx.
In the vertical axis, 12mm wide steel bars are used to tie the top ring to the bottom ring. These are in turn put under tension to not only provide additional stiffness across the structure, but also damping of resonant energy.
The result is a highly inert acoustically silent drum shaped enclosure which eliminates the common issue with subwoofer designs that suffer with so called “subwoofer droning”.
… the IGx blended with the Omnium absolutely seamlessly, making the entire speaker system sound “of a piece” to a degree I haven’t heard from other four-piece speaker systems. The IGx is very subtle sonically, but the musical effect is profound, adding back the missing tonal foundation of the Omnium alone. The IGx also expanded the sense of space that comes from reproducing low-frequency spatial cues.
Robert Harley, The Absolute Sound, USA
Technical Specification
DRIVE TECHNOLOGY | Diaphragm | 18” Carbon Fibre – Polyethylene Terephthalate (PET) |
Core | Large Steel Core, Housing 2x Voice Coils, 2x NdFeB High Power Magnets in Push-Pull Formation | |
INTERFACE GAIN | -30dB to +45dB | |
OUTPUT POWER | 100W Continuous 500W Max into 4Ω | |
FREQUENCY RESPONSE | 12Hz to 90Hz Max (-3dB) 12Hz to 30Hz Min (-3dB) | |
INPUT IMPEDANCE | 10k ohms (RCA) 10k ohms per phase (XLR) 180k ohms (Speakon) | |
DISTORTION (THD) | < 0.04% @1W | |
PHASE SHIFT | Balanced passive all-pass filter (0°-deg to 180° | |
PHASE SHIFT BYPASS | Panel mounted toggle switch (Direct or Variable phase) | |
ANALOGUE INPUTS | 1 x Left RCA 1 x Left XLR 1 x Right RCA 1 x Right XLR 1 x Left & Right High level Speakon | |
INPUT SENSITIVITY | 500mV (Low level unbalanced RCA) 250mV per phase (Low level balanced XLR) 5V (High level Speakon) | |
POWER CONSUMPTION | 10W-15W (idle) 650W maximum | |
INPUT VOLTAGE FUSE RATING | 230Vac (50/60Hz) UK // 115Vac (50/60Hz) USA | |
FUSE RATING | T2A 250V UK // T4A 110V USA | |
DIMENSIONS | Height | 432mm (17”) inc. spikes |
Diameter | 510mm (20″) | |
Depth | 368mm (14.48”) | |
Weight | 54kg (119lbs) | |
Magnetic Grille Weight | 3kg (6.6lbs) |